Best Practices for Designing Efficient and Reliable Gears
Author Gear Technology India on June 19, 2023
Gears are an essential component of many machines, from automobiles to industrial machinery. The efficiency and reliability of these machines depend heavily on the design of the gears
By: Nishant Kashyap
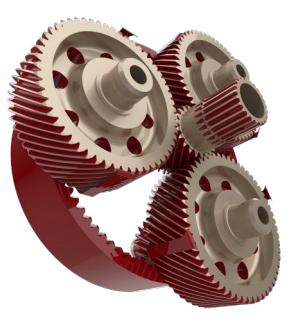
Choose the Right Gear Type
Choosing the right gear type is crucial for designing efficient and reliable gears. There are various gear types available such as spur gears, helical gears, bevel gears, and worm gears. Each type of gear has its own advantages and disadvantages.
For instance, spur gears are the most common and economical, while helical gears offer more contact area, resulting in smoother and quieter operation. Bevel gears are suitable for transmitting motion between intersecting shafts, and worm gears are best suited for high torque applications.
Understanding the requirements of the gear system and selecting the right gear type can improve gear efficiency and reliability.
Material Selection
The characteristics of using high-quality materials for gears are high strength, good wear resistance, and high fatigue strength. Commonly used materials for gears include alloy steel, stainless steel, and bronze.
The material selection should be based on the application requirements and environmental conditions. By using high-quality materials, this will improve gear durability, reduce wear, and increase gear life.
Gear Geometry
The geometry of gears plays an important role in their performance. The gear tooth profile and the pitch diameter are critical factors that affect the efficiency and reliability of gears.
The gear tooth profile should be designed to minimize contact stress and provide maximum load-carrying capacity. The pitch diameter should be optimized to achieve the desired gear ratio while ensuring the gears are not too small or too large in size. Optimizing gear geometry can improve gear efficiency, reduce wear, and increase gear life.
Lubrication
Proper lubrication is critical for the efficient and reliable operation of gears. Lubrication helps to reduce friction, wear, and heat generation. The lubricant used should have the right viscosity and be able to withstand the operating conditions of the gear system.
Over-lubrication or under-lubrication can cause gear failure. It is important to ensure that the gear system is properly lubricated at all times for it to function optimally.
Heat Treatment
Heat treatment is used to improve the mechanical properties of gears. The most common heat treatment processes are quenching and tempering. Quenching involves rapid cooling of the gear from a high temperature, while tempering involves reheating the gear to a lower temperature.
The heat treatment process should be optimized to provide the required strength and durability while minimizing distortion.
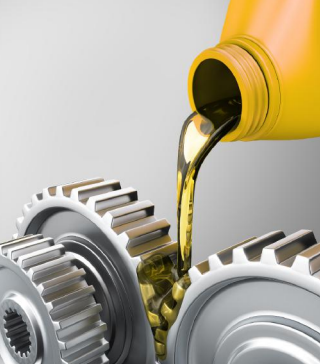
Precise Manufacturing
Manufacturing tolerances are the allowable variations in the dimensions of the gear. These tolerances are critical for achieving proper fit and ensuring smooth operation. The manufacturing process should be designed to minimize the tolerances and ensure that the gear is within the specified tolerance range.
The manufacturing process should ensure that the gears are accurately produced with the correct tooth profile and pitch diameter. Any deviations in the manufacturing process can result in reduced gear efficiency and reliability. The use of modern manufacturing technologies such as CNC machining, gear hobbing, and gear shaping can improve the accuracy and consistency of gear manufacturing.
Regular Maintenance
Quality control is essential for ensuring that the gears meet the required specifications. This involves inspection and testing of the gears to ensure that they are within the specified tolerances and meet the required mechanical properties.
Regular maintenance is crucial for ensuring the efficient and reliable operation of gears. The gear system should be inspected periodically for any signs of wear or damage.
Any worn or damaged gears should be replaced immediately to prevent further damage to the gear system. Proper maintenance also includes proper lubrication, cleaning, and inspection of the gear system. Regular maintenance can help to extend gear life and prevent gear failure.
Conclusion
Designing efficient and reliable gears requires a comprehensive understanding of the application, material selection, gear geometry, lubrication, heat treatment, manufacturing tolerances, and quality control.
By following these best practices, engineers can design gears that provide the required performance, durability, and reliability leading to the success of a machine.
Post Views: 783