Spraying to All Fields: Catching Up on Some Lubrication Trends and Issues
Author Gear Technology India on June 16, 2023
By: Jack McGuinn
Lubrication — as it pertains to the gear industry — is a rather large universe, much, much more than the old double-entendre “the squeaky wheel gets the grease.”
Indeed, lubrication in this universe encompasses gear oils, coolants, greases, oils and sophisticated lubricants — intended for everything gear-related from bearings to gearboxes to pinions to couplings to machinery, and more. Add in the lubrication equipment — some of it quite sophisticated — used to deliver these various lubricants — including synthetics — to where they need to go, and it’s easy to understand there’s a lot going on.
To try and bring some clarity to the situation, we enlisted several experts to offer their thoughts on a number of issues addressing lubrication. It’s a general approach to seeking information on the current trends and challenges inherently relevant to lubrication technology and its ever-evolving development and usage.
Synthetic lubricants are now a front-and-center issue in the industry. The question that this presents is whether there is an industry-recognized definition of a “synthetic” lubricant.
As you might expect, it’s more complicated than trying to decide whether using a synthetic for your next oil change is a good idea. “In Germany they define a synthetic PAO as 100% PAO,” says Robert XX Errichello, president of GEARTECH. “In the U.S. and elsewhere, a synthetic PAO can be a blend of 1-30% PAO and mineral oil. Sometimes these PAOs are called semi-synthetic. PAG is considered synthetic oil in every country (Ref. 1).
Meanwhile, according to René Greschert, WZL gear testing engineer, “There has already been a legal dispute about (this) — but no industry-recognized standard. Therefore, the term ‘synthetic’ is used very creatively. However, completely chemically formulated oils are mostly referred as “full synthetic,” (i.e. — mixtures of full synthetic) and mineral oils as “semi-synthetic.” On the other hand, even hydro-crack oils, which are actually based on mineral oils, are often advertised as “HC-synthesis,” probably to make them appear more valuable.”
Fixed viscosity grades are another key consideration for lubricants — particularly relevant to micropitting protection. The question: what works best?
“PAG has the highest micropitting resistance, and mineral and PAO have less — but similar — micropitting resistance,” says Errichello. While on one hand Aaron Isaacson, Senior Research Engineer and Head of the Drivetrain Technology Center at the Applied Research Laboratory of The Pennsylvania State University and Managing Director of the Gear Research Institute, states, “I wouldn’t think that film thickness would depend on base stock.”
Greschert offers that “The tendency for micropitting resistance and gearbox efficiency (correlates) with the EHL film thickness,” adding, “therefore, the lubricant performance tends to improve in the order of mineral – PAO – PAG. However, it is possible to observe different trends in practice, since the lubrication is also affected by other factors as, for example, the additives of the lubricant as well as by their complex interdependencies and side effects.”
Relatedly, EHL film thickness is another crucial component of lubrication. It requires determining the correct base stock (mineral, PAO, or PAG) for use in the application. “It depends on the gear tooth temperature,” Errichello states. “PAG has thicker films than PAO and mineral over the entire range of practical temperature. There is little difference between PAO and mineral for the range of 70-90°C. At < 70°C, mineral and PAG have thicker films than PAO. At >90°C, PAO and PAG have thicker films than mineral (Ref. 2).
Gearbox efficiency is a condition that is constantly under industry-wide pressure for improvement. Expectedly, lubrication plays a significant role in that improvement. And what lubrication parameter has the greatest impact on that efficiency?
“There are many ways to increase the efficiency of a gearbox,” says Isaacson. “Generally, you want to decrease losses. Losses are due to friction, churning, and/or windage. Friction can be reduced by a number of methods — such as reducing surface roughness, adding low-friction coatings to rolling/sliding components such as gears and bearings, adding additives to the lubricant, and probably a handful more.
Churning losses can be reduced by using a lower- viscosity lubricant, running at a higher lubricant temperature, or reducing the level of oil that rotating parts are forced to churn through. Windage losses can be reduced in jet-lubricated gearboxes by incorporating shrouding around the gears or adding drag-reducing features (air foil winglets!) to the gear design.”
Errichello adds that “PAG has the lowest traction coefficient and therefore gives the highest efficiency. PAG with low viscosity and low traction coefficient generally result in the highest efficiency.”
Relatedly, Greschert adds that “On the one hand, the viscosity grade is predominantly correlating with the no-load losses of a gearbox. Higher viscosity leads to higher churning losses and thus less efficiency. On the other hand, the choice of base oil and additives affects the lubrication regime especially concerning the load-dependent losses of a gearbox. In this context, PAG are reported to perform better than PAO and mineral oils.
One possible explanation for that differentiation between the base oils is their different potential to establish elastohydrodynamic lubrication (EHL) instead of mixed lubrication.”
Not surprisingly, a robust maintenance regimen is required for consistent-performance lubrication. Without it, downtime and costly repairs are in your future. So what constitutes robust maintenance?
“The basic laboratory tests are viscosity, acid number, water content, and spectrometric analysis,” says Errichello. “If questions arise from the basic tests, other tests such as ferrographic, particle counts, and ferrous debris by PQ analyzer should be done.”
“It really depends on your application,” says Isaacson. “Are you generating a lot of debris or particulate? If so, then you’ll likely want to monitor particle counts. Are you operating at high temperatures? If so, you may want to monitor the viscosity and additive contents. Are you concerned about picking up water content or other contaminants? If so, they you’ll likely want to test for those. A great deal can be learned by partnering with a knowledgeable oil analysis company to recommend the proper tests and sampling intervals for your application. Interpretation of results is also not always straightforward. So, having a test lab that understands your goals is a must.”
Finally, manufacturing processes and attendant requirements continue to advance at seemingly break-neck speed. Lubrication is no exception.
“Currently, lubricants and additives are quite good and should continue to improve in the future,” Isaacson says. “Current research areas include nanoparticle additives, ionic lubricants, graphene- based friction reducers, ZDDP additive optimization, viscosity index improvers and a long list of others — any number of which could result in the next big breakthrough in lubrication technology. However, your previous question on preventive maintenance would be where I would focus my efforts. Implementation of a lubrication monitoring system or routine sampling schedule will provide immediate payoff, whereas waiting for the next big thing could take a while.”
WZL’s Greschert explains, “We are currently observing efforts to optimize lubricant compatibility and to expand its functionality. Compatibility requirements are increasing as a result of legal standards (e.g. — compatibility with human organisms), or as a result of a more universal area of application (e.g. — compatibility with sealing elements). For example, metalworking fluids are more and more containing amounts of high-tech synthetic ester oils with excellent performance and sealing compatibility. However, machine tool manufacturers and users are very cautious in using them due to their bad experiences with the first naturally produced ester oils in the 1990’s.
“Another interesting topic is the improvement or substitution of the run-in procedure at the beginning of the application. The most changes to the surface zone of a gear take place at the very beginning of its operation, e.g. — the surface roughness gets flattened, the microstructure is becoming fine-grained and the chemical composition is changed. We’ve had a big research program 2012-2018 (and a continuation starting in 2020 is planned) of more than 20 institutes trying to understand and improve the run-in procedure and its working mechanisms to improve the resource efficiency in the application of lubricants and machine elements.” And, “Yes,” says Errichello, “electric vehicles require special lubricants because the lubricant acts as a coolant to cool the electric motor in addition to lubricating the gears and rolling element bearings in the gearbox. Because of the extreme heat in the motor, mineral, PAO, and PAG do not have the desired properties. This is currently a hot research topic. Perhaps a poly ester fluid, which has superior high temperature performance and increased lubricity that increases efficiency might fill the bill.”
References
1. Swedberg, S., “Motor Oil’s Day in Court,” Lubes’N’Greases, Vol. 20, No. 4, April 2014, pp. 6-13.
2. Errichello, R., “Selecting Oils with High Pressure-Viscosity Coefficient- Increase Bearing Life by More than Four Times,” Machinery Lubrication, Vol. 4, No. 2, Mar/Apr 2004, pp. 48-52.
Robert Errichello is president of Geartech,
and can be reached at rlegears@mt.net.
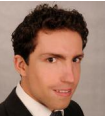
Dr.-Ing. René Greschert, is a gear testing
engineer at WZL (Laboratory for Machine
Tools and Production Engineering), RWTH
Aachen University. He can be reached at
R.Greschert@wzl.rwth-aachen.de.
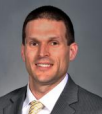
Aaron Isaacson is a Senior Research
Engineer and Head of the Drivetrain
Technology Center at the Applied Research Laboratory of The Pennsylvania
State University and Managing Director
of the Gear Research Institute. He can be
reached at aci101@arl.psu.edu.
Post Views: 565