Recent Advances in the Evolution of Gear Technology in the Power Sector
Author Gear Technology India on June 19, 2023
With ongoing advancements in technology and materials, it’s an exciting time to be involved in the world of gear manufacturing and power generation
By: Sushmita Das
The use of gear technology has been an integral part of the power sector for many years. From the earliest water and windmills to the most advanced power plants of today, gears have played a critical role in converting rotational motion into useful energy.
As the power sector continues to evolve, so does the technology that drives it. Here, we will take a closer look at recent advances in gear technology and its significant impact on the power sector.
As per a report by Research and Markets, the worldwide market for industrial gearboxes attained a valuation of USD 24.90 billion in 2020 and is anticipated to exhibit a CAGR of 4.20% over a forecast period between 2021-2026, culminating in a market worth USD 31.31 billion by 2026.
3D Printing
One of the most significant recent advances in gear technology is the use of 3D printing. With this technology, gears can be designed and produced with much greater precision and complexity than traditional manufacturing methods. This allows for more efficient and compact gear designs that can lead to significant energy savings in power plants.
Additive manufacturing has also enabled the creation of lighter, stronger, and more durable gear components, which can improve efficiency and reduce maintenance costs in power generation systems.
The ability to create customized gears using 3D printing has led to improved performance and reduced downtime in power generation systems.
Advanced Materials
Materials like the use of carbon fiber and ceramics have also contributed to the gear development technology.
These materials offer significant advantages over traditional metals in terms of weight, strength, and durability. This allows for the creation of lighter and more efficient gear designs that can handle higher loads and operate at higher speeds.
Nanoparticle-based lubricants are being developed for gear applications, providing improved lubrication and reducing friction, which can result in higher efficiency and longer gear life.
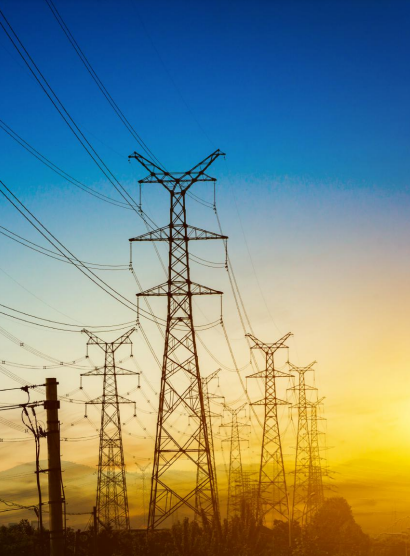
Software and Simulation Tools
With these tools, engineers can model and test gear designs in virtual environments that allows for more efficient and cost-effective design iterations. This can lead to faster development cycles, lower costs, and higher overall performance.
Trends
In addition to these technological advances, there has also been a growing trend towards more sustainable and environmentally friendly gear designs in the power sector.
For example, the use of regenerative braking systems in wind turbines and electric vehicles can help to reduce energy waste and improve overall efficiency.
The power sector has also embraced digitalization and the Internet of Things (IoT), which has led to the development of smart gears that can monitor and optimize performance in real time.
Conclusion
Looking ahead, it’s clear that gear technology will continue to play a critical role in the power sector.
As new sources of renewable energy are developed and the demand for clean, efficient power continues to grow, the need for advanced gear designs and manufacturing methods will only increase.
Post Views: 522