Balaji Diamond Tools: Driving Excellence in Gear Grinding Technology
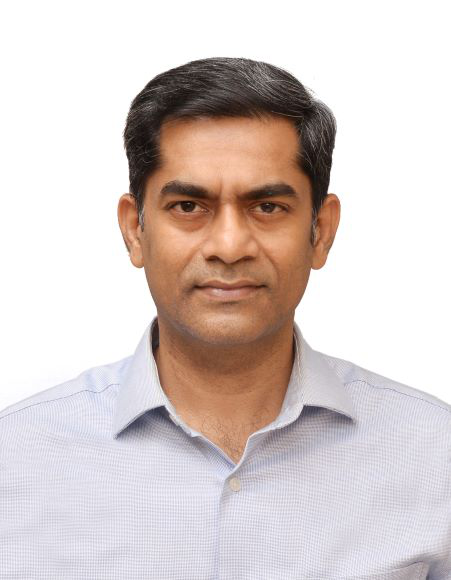
B. Praveen Kumar
CEO - Balaji Diamond Tools
Author Sushmita Das on September 13, 2024
Introducing B. Praveen Kumar, the dynamic CEO of Balaji Diamond Tools, a leading innovator in the gear grinding industry. Under his leadership, the company has made significant strides in developing specialized diamond tooling solutions that cater to the unique needs of precision-driven sectors like gear manufacturing.
In this interview, Mr. Praveen Kumar sheds light on how Balaji Diamond Tools is meeting the evolving demands of the gear grinding industry through cutting-edge products, customized solutions, and a relentless focus on quality. He also discusses recent innovations, such as the introduction of CVD single-edge dressing tools, which are designed to enhance consistency and accuracy in gear grinding applications. Moreover, he explores how the company’s research and development team continuously innovates to address customer challenges and stay ahead of industry trends.
From quality control measures to the role of advanced diamond and CBN wheels in improving grinding efficiency, Mr. Praveen Kumar provides valuable insights into how Balaji Diamond Tools remains at the forefront of gear grinding technology. As the conversation unfolds, we gain a deeper understanding of the company’s commitment to excellence and its vision for the future of gear grinding.
- How does Balaji Diamond Tools cater to the specific needs of the gear grinding industry with its product range?
As a first step, we understand the customer’s application regarding the finish and desired tolerances for the job. Further, we recommended an appropriate diamond tooling solution to the customer.
- Can you elaborate on any recent innovations or advancements Balaji Diamond Tools has made in the field of gear grinding?
We have developed a CVD single-edge dressing tool, which is a great solution for precision jobs, especially gear-grinding applications. This product delivers consistency in finish and accuracy, which is a fundamental expectation of the gear-grinding industry.
This tool is a great alternative for natural single-point diamond dressers – which overwear and tear will lead to deviations in finishing/accuracy also the top quality diamonds are proving expensive, which the industry can’t afford to pay such high prices given the limitations and constraints of the industry.
- How does the company handle customized tool requests for gear grinding applications, and can you share some examples of unique solutions provided?
We have a tool selection chart which defines the choice of tool for the said grinding application.
Secondly, the raw material grades are chosen based on customer requirements in terms of Ra value and tolerance.
Every industry and shop floor has a unique requirement, so it’s not the case that one tool fits all requirements.
- What specific quality control measures are in place to ensure the precision and reliability of your gear grinding tools?
Our quality check is done at every stage of the production. Our products are processed as per BIS & DIN standards (roller dressers are made with German collaboration)
- How do your diamond and CBN resin and metal bond wheels enhance the efficiency and accuracy of gear grinding processes?
Diamond wheels are employed for carbide grinding applications. Whereas the CBN wheels are used for hardened steel of above 45hrc grinding applications.
Diamond | CBN wheels ensure dimensional accuracy of around 3 to 5 microns and a high finish with a Ra value of 0.1–0.2. Which is quite difficult to achieve with bonded abrasives.
- Can you discuss the role of your R&D team in developing new gear-grinding technologies and tools?
As and when a customer issue or problem statement is received, we look at possible solutions by tweaking the bond combinations, grit structural sizes, and grades to overcome the problem/issue. The R & D team is in a continuous process to keep developing different combination products through several iterations and provide the best possible tools/solutions.
- What are some common challenges faced in gear grinding, and how do your products address these issues?
Primarily we witness that the customer has a world-class grinding machine, and world-class abrasive wheels, but unfortunately, quite sometimes they are not complemented with the right quality diamond tool which will ultimately reflect the finish and accuracy of the product.
We do our best to share our expertise in the choice of selection of the right type & grade of diamond tools/wheels to meet the expectations of the user.
- How does Balaji Diamond Tools stay updated with the latest trends and demands in the gear-grinding industry?
We work with our principals in the industry and constant sharing of knowledge happens through international conclaves and conferences.
- How do you incorporate customer feedback into the design and manufacturing of your gear grinding tools?
Most of the design is provided by the customer. As our products are consumables, the design is usually provided by the machinery manufacturer.
- What future developments or product launches can we expect from Balaji Diamond Tools in the context of gear-grinding technology?
We intend to develop special bonds and diamond coating methods for robotic operations, creep grinding operations and intricate profile grinding.
-
Sushmita Das is an accomplished technical
writer. Holding a degree in Electrical Instrumentation and Control System Engineering,
she brings a wealth of technical expertise to
her writing
View all posts
Post Views: 127