Driving Innovation and Efficiency in the Gear Industry
Author Gear Technology India on June 19, 2023
From additive manufacturing to advanced machining processes, gear manufacturing technologies are paving the way for a new era of innovation and excellence
By: Sushmita Das
The gear manufacturing industry has witnessed a significant transformation in recent years, thanks to groundbreaking advancements in manufacturing technologies. These innovative techniques are revolutionizing the production of gears, enabling manufacturers to meet the growing demands for efficiency, precision, and customization.
Additive Manufacturing: Redefining Gear Production Possibilities
Additive manufacturing, also known as 3D printing, has emerged as a game-changer in the gear manufacturing sector. This technology allows for the creation of complex gear geometries that were previously difficult or impossible to achieve using traditional manufacturing methods. With additive manufacturing, gears can be produced with intricate internal structures, custom teeth profiles, and optimized weight distribution.
One of the significant advantages of additive manufacturing in gear production is its ability to reduce material waste. By building gears layer by layer using only the necessary material, manufacturers can minimize material usage, leading to cost savings and environmental sustainability.
Furthermore, the flexibility offered by additive manufacturing enables rapid prototyping and customization allowing gears to be tailored to specific applications and requirements.
Advanced Machining Techniques: Precision and Efficiency Unleashed
Traditional machining techniques have also undergone significant advancements, enabling manufacturers to achieve higher levels of precision and efficiency in gear production. Computer Numerical Control (CNC) machining, for instance, has revolutionized the way gears are manufactured. By utilizing CNC machining, this ensures exceptional accuracy, consistency, and repeatability in gear production.
Additionally, advancements in multi-axis machining have opened up new possibilities for gear manufacturing. Multi-axis machines can produce gears with complex geometries and intricate tooth profiles, expanding the design and application options for gears. The ability to machine gears from a variety of materials including metals, alloys, and composites, further enhances the versatility and performance of gears in different industries.

Gear Hobbing and Shaping: Traditional Techniques Evolved
While additive manufacturing and advanced machining techniques have gained prominence, traditional gear manufacturing methods such as gear hobbing and shaping continue to play a crucial role in the industry. These techniques have evolved to meet the demands of modern gear applications, incorporating automation, computer controls, and advanced tooling systems.
Gear hobbing, a well-established method, involves cutting gear teeth using a specialized hob. Modern gear hobbing machines offer high precision, allowing manufacturers to produce gears with tight tolerances and smooth tooth profiles. Gear shaping, on the other hand, utilizes a cutting tool to form gear teeth gradually.
This technique is often preferred for producing gears with large diameters or when high accuracy is required.
Digitalization and Simulation: Enhancing Efficiency and Performance
The integration of digitalization and simulation tools has enabled manufacturers to optimize production and enhance gear performance. Computer-aided design (CAD) software allows for precise gear design, with virtual simulations enabling engineers to analyze and fine-tune gear performance before physical production.
Simulation software helps identify potential issues such as tooth contact errors, gear misalignment, or noise generation, allowing for optimization and refinement before gears are manufactured. These digital tools reduce the time and cost associated with physical prototyping, while also minimizing the risk of defects and errors during gear production.
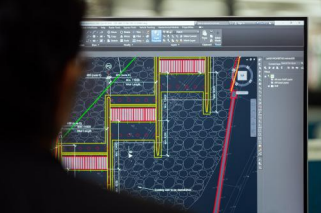
Conclusion
The gear manufacturing industry is undergoing a remarkable transformation driven by advanced manufacturing technologies that are pushing the boundaries of what is possible. Additive manufacturing, advanced machining techniques, traditional methods, and digitalization tools are collectively revolutionizing the production of gears, resulting in higher precision, customization, and efficiency.
As these technologies continue to evolve, the gear manufacturing industry is poised to meet the increasing demands of various sectors, driving innovation and propelling industries towards a more advanced and efficient future.
Post Views: 638